Innovations
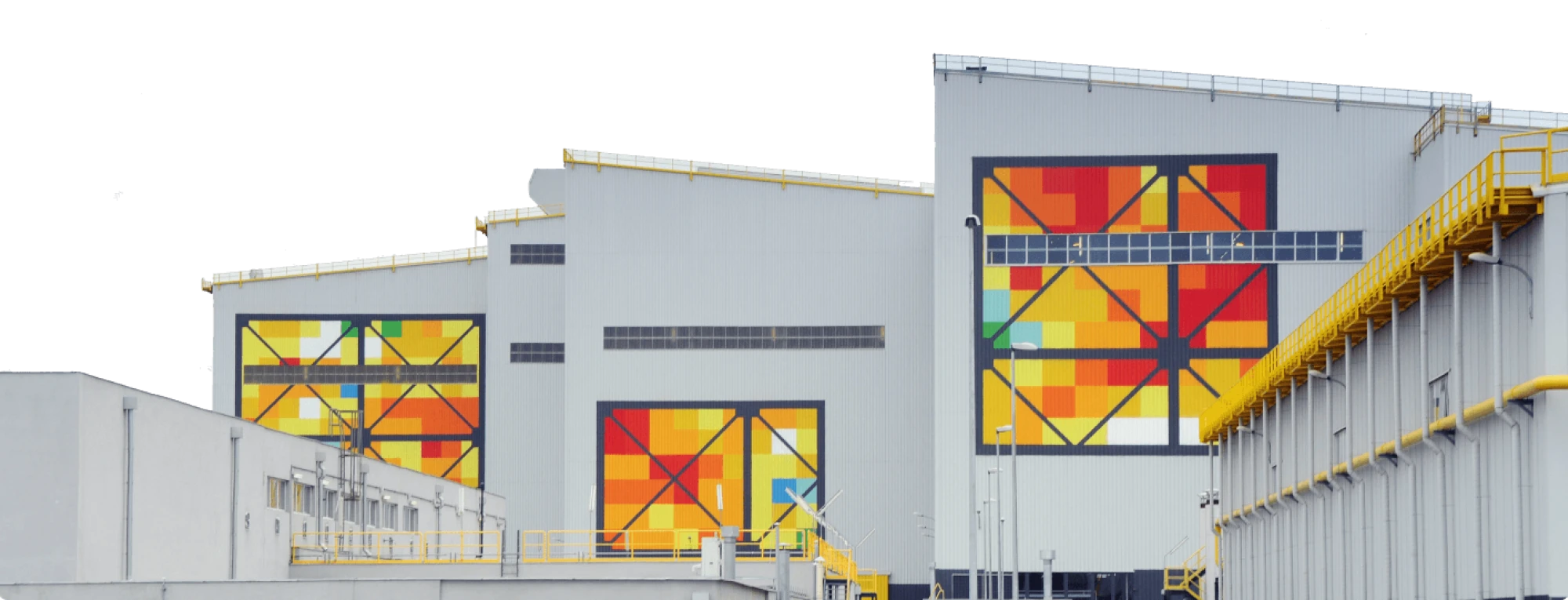
Interpipe Steel is the only Steel plant built from scratch since Ukraine's independence. It is the largest environmental investment in the country's industry. Interpipe invested $1 billion in the construction of an innovative electric steel-melting complex, which allowed the company to close down its outdated, environmentally polluting open-hearth production. As a result, CO2 emissions were reduced by 10 times and natural gas consumption, by 8 times.
Equipment for the new plant was supplied by the Italian company Danieli, one of the world's largest suppliers of modern solutions for the Steel industry. In line with the Company's vertical integration, Interpipe Steel fully meets the billet supply needs of Interpipe's pipe and wheel production. Innovative steel-melting technologies and full automation of all processes make it possible to produce the most complex steel grades in an environmentally friendly manner.
The construction of Interpipe Steel was partially financed by loans from the Italian export credit agency SACE. As part of its cooperation with SACE, Interpipe confirmed the plant's compliance with European environmental requirements at every construction stage. Even after the project was completed, the plant underwent an environmental audit by EU experts every six months. Today, Interpipe Steel meets the Green Deal targets for 2050 in terms of CO2 emissions: up to 250 kg per tonne of steel.
In all developed countries, according to Worldsteel, the share of electrometallurgy in total steel production is either dominant or significant. The Middle East (94%), the US (71%) and Turkey (69%) are the leaders in this sector. In the terms of green transition, the concept of building electric steel plants or mini-mills is gaining popularity in Europe, where the share of electric metallurgy is still slightly above 40%. For example, there is a steel plant in the tourist centre of Italy, city of Udine near Venice, that is a perfect analogue of Interpipe Steel. It does not scare away tourists and has no impact on the environment.
That is why today Interpipe Steel is a benchmark not only for the further development of the national green steel industry, but also for the large-scale environmental transformation of the entire Ukrainian economy.
Interpipe Steel is distinguished not only by state-of-the-art metallurgy technologies and stringent environmental standards, but also by its unique production culture. A zoning system with divisions such as a home clothes zone, a hygiene zone and a workwear zone was implemented at the company's premises. A comfortable, modern canteen was created for the staff.
In addition, the company has 5 art installations by Danish-Icelandic artist Ólafur Elíasson that fuse modern production and contemporary art. The most famous artwork, the 60-metre-tall Dnipro Sunrise, symbolises Ukraine's industrial revival.
Interpipe has been digitally transforming its processes and investing in Industry 4.0 technologies for over 10 years. The key goal is to use resources efficiently, meet customer requirements and successfully compete in export markets.
All of the Company's assets have a single ERP system for managing production, sales, finance, human resources, equipment repair and maintenance and procurement.
An integrated financial system and treasury:
- accounting consolidation and centralisation
- cash flow and accounts payable management
- operational accounting of actual costs of primary and auxiliary production
- calculation of the cost of each technological operation
- integrates industrial assets, centralised services and foreign sales offices
- a single payment factory for all financial, commodity and production operations
- machine learning allows the system to automatically generate outgoing documentation
Traceability, production planning and management:
- an integrated order register for end-to-end work with each order and reduced processing time
- 100% online accounting of steel billet and pipe production at pilot sites
- complete online catalogue of work in progress at pilot sites
- optimised production schedules and reduced equipment downtime
- automated scheduling allows for effective deadline control at all production stages
Predictive equipment maintenance:
- a new approach to equipment maintenance based on Predictive Maintenance and RCM (Reliability Centred Maintenance) methodology
- complete equipment e-catalogue
- predictive equipment diagnostics
- big data analysis for repair scheduling, equipment maintenance and spare part procurement
- implemented Smart.EAM Mobile App for organising examinations, inspections and request generation
Warehouse Management System:
- an integrated database of finished products at the implemented sites
- an integrated warehouse location (pocket) system
- automated transport batch creation
- IIoT technologies for prompt shipment
- reduced vehicle downtime by 3 times
Logistics Digitalisation:
- order and transport information in an integrated system
- control of the vehicle time spent on the plant territory
- GPS monitoring system along the entire route
- timely rearrangement of shipment time with the customers in case of delay / advancement of the schedule
- manual control of only those vehicles that are critically behind the delivery deadlines
- reduced volume of operational work of the logistics service
- using an online tender platform makes it easier to choose a carrier
Electronic Document Flow:
- 100% online tender procedures
- some documents have already been converted into electronic format with digital signatures
- automated document generation in the ERP system
- external online document management with contractors and suppliers using the Signy.Online module
Product Portfolio: Innovative Designs
Premium solutions for oil and gas production
Premium railway wheels for freight transport
Interpipe has an R&D centre that develops and improves its product portfolio to meet the growing demands of its customers.
The company offers a range of premium connections for the development of oil and gas wells in difficult geological conditions with high compressive and tensile loads:
The Company's technical experts developed a new solution for safe operation of freight cars with increased loads. The Ultimate line of wheels and wheelsets with low-stress discs are designed specifically for the European market and provide high performance. In addition, it is a low-noise product line that meets all European requirements.
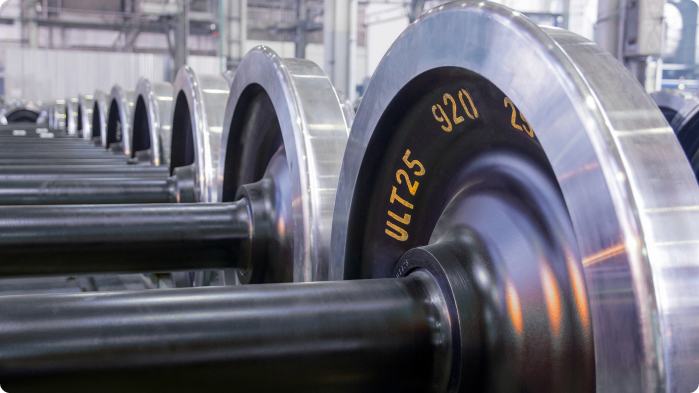